Analysis of the costs linked to the purchase of a collector figurine: between art and Science, a fantastic journey
- STÉPHANE LACROUX
- Feb 2, 2024
- 6 min read

From the idea to the tangible figurine: Analysis of the purchase of a collector figurine
Creating a figurine is a fascinating process that skillfully mixes art, technique and passion. This journey begins with an idea, concept or emotion and transforms into a tangible work, each step requiring dedication, sensitivity and skill. Let's discover together the secrets of making a figurine, from the initial sketch to the finished piece, including the multiple stages that define its cost and value. Let's go !
Design: The Emergence of the Idea
It all starts with design. This crucial phase involves the creation of drawings and sketches, where ideas take shape. I have to study the character from all angles, establish his pose and capture his essence in every feature. This involves extensive research, detailed sketches and reflection on its concept so that the initial vision is faithfully transposed into a 3D model.
This is not a “quickly done, well done” figurine, no! The idea is to convey an emotion, a story.
3D Modeling: Digital Sculpture
3D modeling transforms the sketches into a three-dimensional digital model (wow, we’re using big words here!). It’s a stage where art meets technology. Advanced software allows you to sculpt every detail with precision, personally I use Z Brush or Blender.
Every accessory, item of clothing, and environment must be meticulously designed to reflect the character's likeness. Of course, some freedom related to the artist's style may be included. In this important step, we must anticipate the fact that the collector figurine must be 3D printable in a suitable machine. Here, we are talking about 3D printing and not the concept of video games which are completely different concepts. It’s therefore a real mental task to have to ask yourself the right questions before making a pose that can be printed in 3D. This process will take place throughout the creation:
- Will this sword be able to be printed? isn't this too thin?
- Are the decorations not too imposing in order to avoid excessive cut-outs?
- Is the thickness of the clothing sufficient to be 3D printed?
You will have understood, modeling is the important step which makes the concept possible, but nevertheless which requires a consensus between imagination and the possibilities of 3D printing.
It is also at this stage that we think about which part of the model will be cut out (arm, leg, coat, sword, etc.), so it will be necessary to add functional inserts.
Optimization for 3D printing: Slicing
Optimizing for 3D printing, known as “slicing,” prepares the figure for 3D printing.
This step transforms the 3D model into instructions (line of code) for the 3D printer. For an original figurine, this means optimizing each part and accessories so that they are 3D printable in resin. Slicing must take into account the feasibility of printing, the capabilities of each 3D printer and each type of resin, avoiding excessive overhangs and ensuring structural stability.
We use several types of resin:
12K resin: 3D resin from Jamg He
Standard resin: 3D resin from Siraya Tech or SUNLU
Fast Resin: Jamg He Ultra Speed Resin
Special Resin: resistant resin from Siraya Tech
Transparent resin: resin from Résione
And many other yet...
Let's continue the cost analysis linked to the purchase of a figurine, from the idea of a figurine to 3D printing.
During the slicing stage, we will optimize the supports, the hollowing if it is possible or necessary, and of course optimize the hollowing holes in order to promote good 3D printing quality.
Cleaning and Polymerization: Grab your gloves and masks!
After printing, the figurine goes through a cleaning phase: we meticulously remove the print supports, being very careful not to break anything like small strands of hair (yes, it smells like a real experience!). Then comes the bath with isopropyl alcohol, it's a big scary word... And you'll be right!
You must protect yourself: a mask and gloves are mandatory, alcohol gives off a strong odor, just like resin which can smell strong during printing. This article aims to inform about all the costs related to 3D printing, and protective equipment is one of them.
Once all the work has been done without having broken a part or without having to reprint the figurine which would not be printed correctly (and yes that is one of the hazards of 3D printing of artisanal figurines!), it is the final step: polymerization of the figurine!
We place the part in a suitable machine with UV LEDs which will finish the work of curing the resin for a variable duration of 5 to 15 min.
Post-processing: Artistic Refinement
Here we are, the figurine is beautiful and very dapper! Should we attack post-processing? Let's go.
Post-treatment, includes sanding with several grains to have the most beautiful surface possible. Once finished we apply a tiny layer of resin, this is essential to obtain a smooth surface ready for painting. This requires an artistic eye and a deft hand, especially for detailed figurines like video game characters, where every texture and detail of the costume must be perfectly smooth and ready for painting.
Painting and Varnishing: Bringing the Figurine to Life
Painting and varnishing are the final touches that bring the figurine to life. This step requires not only sensitivity and artistic skill, but also some skills, particularly in understanding the play of light, textures and nuances. For example, painting a figurine of a fairy requires specific techniques to create effects of light, transparency, and delicate details, like leaves running across her body.
In any case, this requires equipment: brush (and not those from Action which will not have the finesse and quality necessary to have a nice result.), an airbrush for a smooth result and specific effects, paint suitable for figurines like Green Stuff World, Army painter, Valejo, etc. There is a lot of material to have for an artist who sells figurines but a photo speaks louder than words:
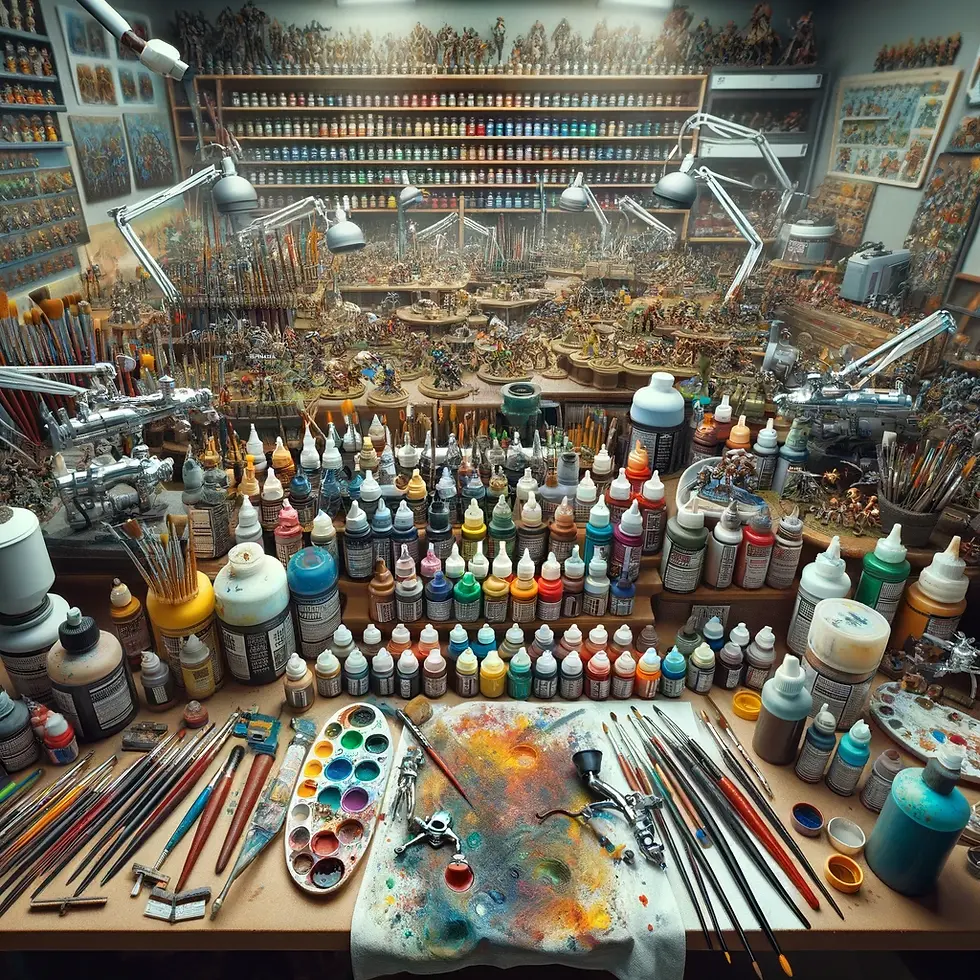
The delivery of the figurine, we're talking about it!
Of course, the figurine is beautiful, finished and ready to be packaged for its lucky owner.
At this stage, you have to be careful not to break the figurine during transport (that would still be a shame). You have to think about the right dimensions of the cardboard, foam, bubbles and other accessories that allow safe delivery.
Conclusion: A Complex Creation Process
In summary, creating a figurine is a complex artistic and technical journey, uniting imagination, skill and attention to detail. From the emergence of the idea, each step is crucial: design, where emotions take shape, 3D modeling which digitizes and affirms the concept, optimization for 3D printing which prepares the model to become tangible, and finally, cleaning and polymerization, key steps to guarantee the quality and durability of the work. The artistic refinement of post-processing and varnishing enhances the figurine, giving each creation a unique soul.
The paint provides the final touch, giving life and character to the object. Finally, delivery, although often overlooked, is essential to ensure that the work of art reaches the hands of its new owner intact.
This process, combining passion and precision, reveals not only the artist's talent, but also his commitment to his passion and his clients, transforming a simple idea into a physical and appreciated work of art.
Analyzing the cost of creating a figurine, as described in the article, reveals the complexity and diversity of expenses involved in this artisanal and artistic process.
Here is a detailed cost breakdown based on the different steps mentioned:
1. Design:
- Research and Design: Time spent on research, designing drawings and sketches. This potentially includes purchasing reference materials or accessing online resources.
- Design Software: Cost of modeling software like Z Brush, which can be in the form of a one-time purchase or monthly/annual subscriptions.
2. 3D modeling:
- Computer Equipment: Cost of a powerful computer capable of managing complex 3D modeling software.
- 3D Modeling Software: Cost of software licenses, which may vary depending on the features and services offered.
3. Optimization for 3D Printing:
- Slicing Software: Costs of specific software for preparing models for printing.
- Consumables: Cost of resins (12K, standard, Rapid, special, transparent, etc.), which varies depending on type and quality.
4. 3D printing:
- Cost of the 3D Printer: Initial investment in the purchase of one or more 3D printers.
- Maintenance and Wear: Regular maintenance costs, replacement of worn parts.
5. Cleaning and Polymerization:
- Cleaning and Curing Equipment: Cost of cleaning and UV curing machines.
- Consumables: Isopropyl alcohol, gloves, masks, and other safety supplies.
- Electricity: Cost of energy to operate this equipment.
6. Post-processing:
- Supplies: Sandpaper, primer, and other materials for sanding and surface preparation.
- Working Time: Hours spent sanding, preparing and refining the figurine.
7. Painting and Varnishing:
- Paints and Varnishes**: Cost of high quality materials for painting and varnishing.
- Equipment: Cost of airbrush and specific brushes.
- Working Time: Hours spent painstakingly painting each figurine.
8. Packaging and Delivery:
- Packaging Materials: Cost of cartons, foam, bubble wrap, etc.
- Shipping costs: Cost of sending the figurine to the customer, which varies depending on distance and weight.
9. General and Unforeseen Costs:
- Workspace: Rent or cost of the workspace used for creating figurines.
- Unforeseen Costs: Breakages, printing errors, or other incidents requiring reprinting or repairs.
This detail shows that each stage of creating a figurine involves not only an investment of time and skill, but also considerable hardware and software costs. This highlights the intrinsic value of each figurine as a unique work of art, reflecting the investment and commitment of the artist.
Yes, there is still the cost of coffee and Nutella toast for all these hours of work ;)
Comentários